We will explain why Toyota Motor Corporation is able to continue producing high-quality products by comparing it to a development flow. I think it can be applied to various technical workplaces, so please refer to it.
- Introduction
- 1. Market research: 36 months before mass production starts
- 2. Design concept: 24 months before mass production starts
- 3. K4 (structural planning): 23 months before mass production starts
- 4. SE (Simultaneous Engineering): 21 months before mass production starts
- 5. Genzu: 20 months before mass production starts
- 6. CV evaluation: 12 months before mass production starts
- 7. Production preparation: 6 months before mass production starts
- 8. Vehicle L/O
- Lastly
Introduction
See the following diagram. This is Toyota’s product development flow. I will explain these one by one.
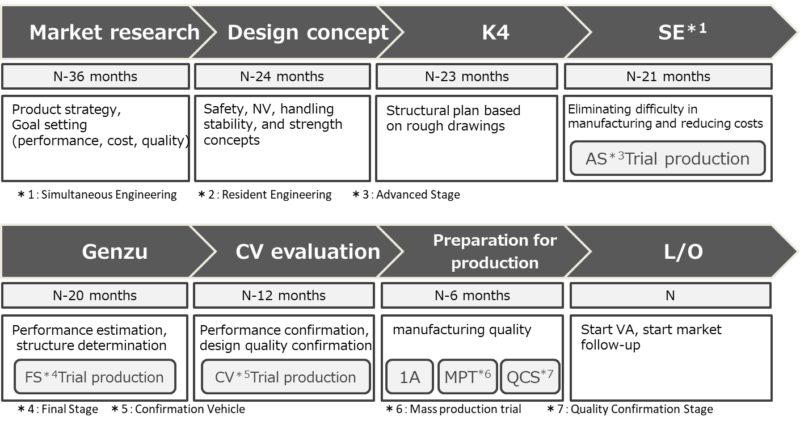
1. Market research: 36 months before mass production starts
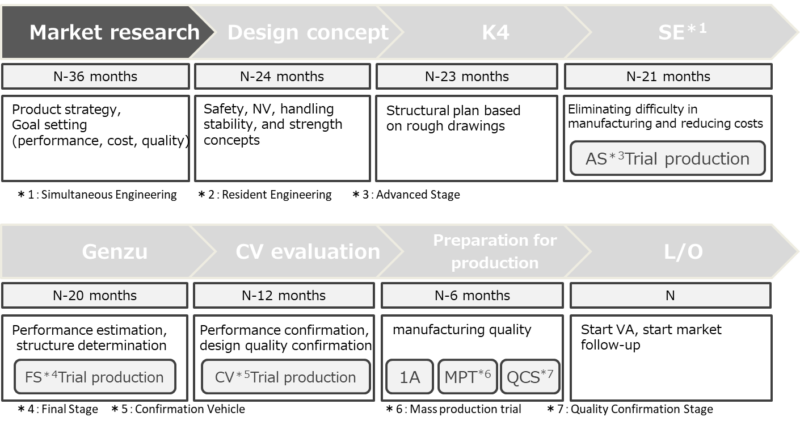
Product planning and the creation of concepts for new vehicle models that precede it are called FSC (Future Scenario Concept). The project begins three to four years before mass production begins, and takes about a year to gather ideas from sales planners and overseas business offices for a car that matches the vision of future society created by the Research Department. Here, we will not refer to specific styling, but rather focus on the perspective of what value should be provided to users.
We then narrow down the concept proposals collected through the open call to three to five and proceed to present them to management. At this point, the appearance is also being considered, and we are in a state where we have a certain idea of what it will look like as a car. After management evaluation, a decision is made between three options: proceeding immediately to development, deferred until next year, or scrapped.
Proposals that pass FSC are handed over to CP (Concept Planner) and proceed to the product planning stage. Product planning begins when a project is actually handed over to the CE (Chief Engineer) who is in charge of engineering, but in reality it seems difficult to clearly separate these two planning stages.
After product planning begins, we determine the target cost, performance, and quality of the product in order to realize the actual product. These target values are set by thoroughly benchmarking the standards of our competitors, predicting future levels (development vehicle L/O period), and allowing us to compete against them.
2. Design concept: 24 months before mass production starts
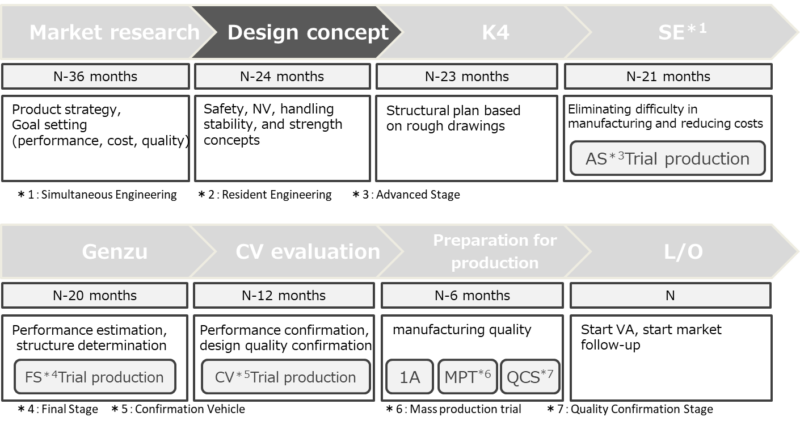
With less than two years until mass production begins, we will enter the design concept stage. Here, we consider from an engineering perspective what level to set the four major performance levels of safety, NV (Noise and Vibration), rigidity (handling stability), and strength.
3. K4 (structural planning): 23 months before mass production starts
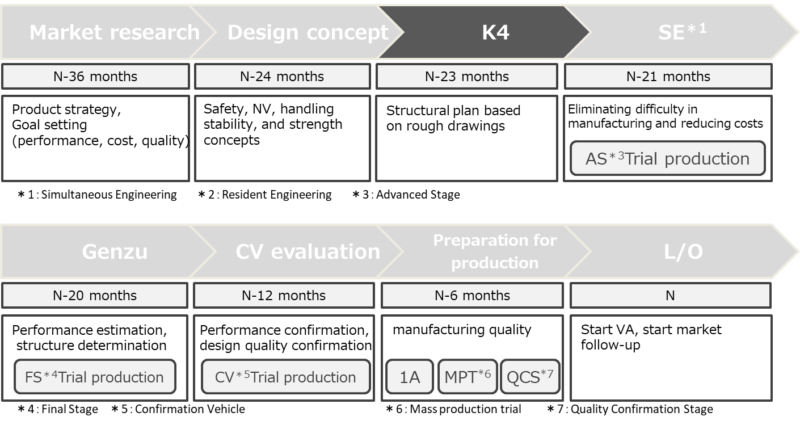
At this stage, consideration begins based on cross-sectional views and punch drawings in order to satisfy various performance requirements. Suppliers are basically not participating at this stage. Therefore, this is a rough study as detailed feedback on manufacturability cannot be provided. However, in order to avoid major mistakes in terms of performance, design estimates are made through desk studies such as similar designs using similar cases.
4. SE (Simultaneous Engineering): 21 months before mass production starts
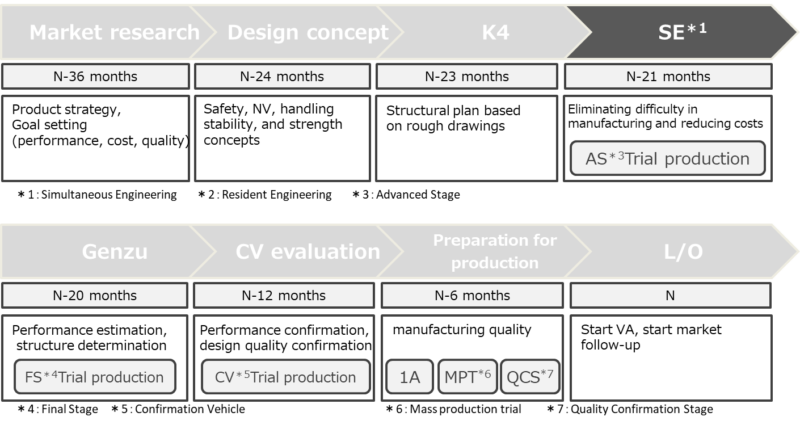
The main purpose at this stage is to evaluate the design quality and “eliminate difficulties in construction.” This is because reviewing product specifications to make them easier for manufacturers is the principle of ensuring consistent and stable manufacturing quality. Another objective is “cost reduction activities.” The design and development department is given strict cost targets in addition to development targets at the planning stage, so the design and development department conducts various studies (VE activities) in order to achieve these cost targets. The production department will also consider its own quality goals and the degree of impact on manufacturing operations, propose cost reduction measures as much as possible by changing specifications, and develop comprehensive cost reduction activities.
From K4 to SE, prototype vehicles are produced at an event called AS (Advanced Stage) to check whether basic performance is satisfied.
The two major features of SE are (1) the participation of outsourcing suppliers, and (2) the participation of the production engineering department.
(1) Participation of outsourcing suppliers
The design itself is often outsourced, leveraging the expertise of component manufacturers. There may be a situation where there are more designers from outsourcing suppliers than employees in the company’s own design department. The key to the success of SE activities is gaining the cooperation of outsourcing suppliers from the early stages of development. SE activities that solidify product specifications at the design and development stage while discussing quality assurance and cost reduction with outsourcing suppliers and in-house manufacturing departments are called “design-in.” .
(2) Participation of the Production Technology Department
This involves bringing forward the work of the factory’s production preparation department to the design and development stage. At each step of development, many organizations related to production become involved. These include the factory’s quality control department and manufacturing department, the production technology department that develops production equipment and methods, and the outsourced suppliers who manufacture parts. These organizations will check the design and development specifications from their respective standpoints and issue requests for improvements.
Since around 1996, Toyota Motor Corporation has been working on collaboration through digital engineering, which they named “V-Comm (Visual & Virtual Communication).” By dramatically improving communication between the pre- and post-processes of vehicle development, we are able to reduce the need to advance solutions to problems identified in the prototype stage to the design stage, improve drawing quality, and reduce development time and costs. This is an activity aimed at achieving this goal. It is called DA (digital assembly) and will be explained using the following typical example.
① Workability DA
We will simulate the worker’s movements using a digital mannequin and check it using a prototype vehicle.
② Appearance DA
We check the appearance of details that cannot be fully examined with mock-ups or partial models, such as the alignment of interior parts and body alignment.
③ Wire harness DA
Wiring harnesses are a difficult subject, and we will now solve the many noise problems that previously had to be solved at the final stage of development.
5. Genzu: 20 months before mass production starts
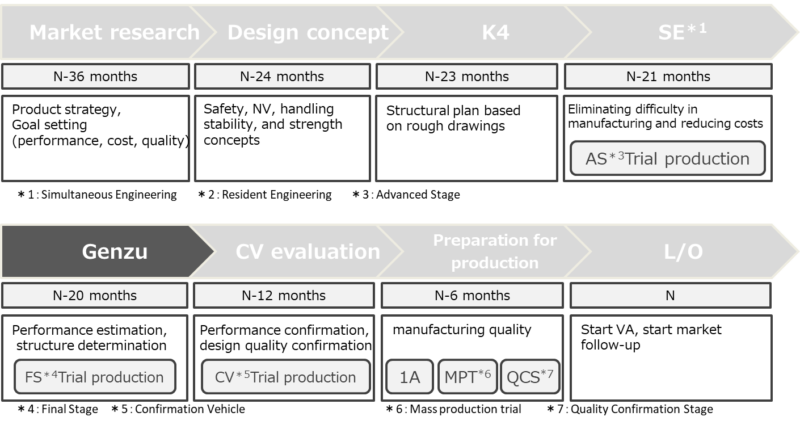
At the next CV (Confirmation Vehicle) prototype event, we will be verifying the performance and quality of this model in a vehicle, so this is the final confirmation step before the supplier prepares for production. Most of the performance and quality have been built in by SE, and this is the final step to ensure manufacturability.
From the SE to the original drawings, a prototype vehicle is produced at an event called FS (Final Stage), and its performance is checked in detail. Nowadays, with improvements in CAE technology, it is now possible to check performance without using the actual machine, so it seems that FS prototyping is no longer being carried out.
6. CV evaluation: 12 months before mass production starts
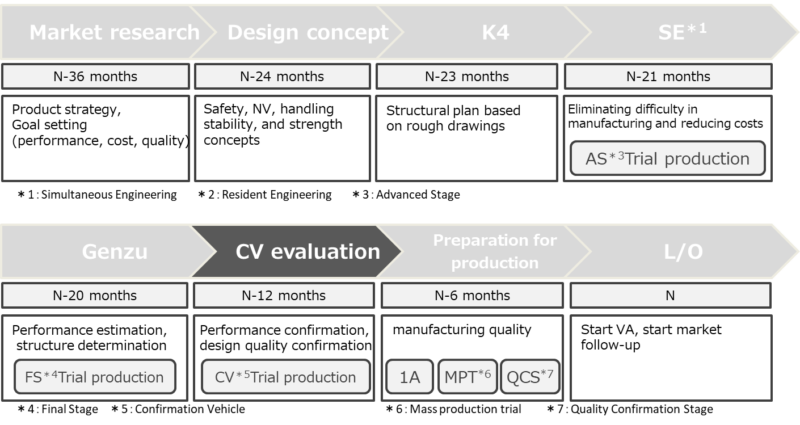
Various tests are conducted using performance verification vehicles using this type of product to check whether the intended performance of the design has been achieved and whether there are any quality problems. We also check productivity for assembly problems at the factory.
The reason why this type of product is required here is to build quality. When entering the next production plan, the technical department will be handed over to the manufacturing department, so any technical design changes must be incorporated into the production plan.
7. Production preparation: 6 months before mass production starts
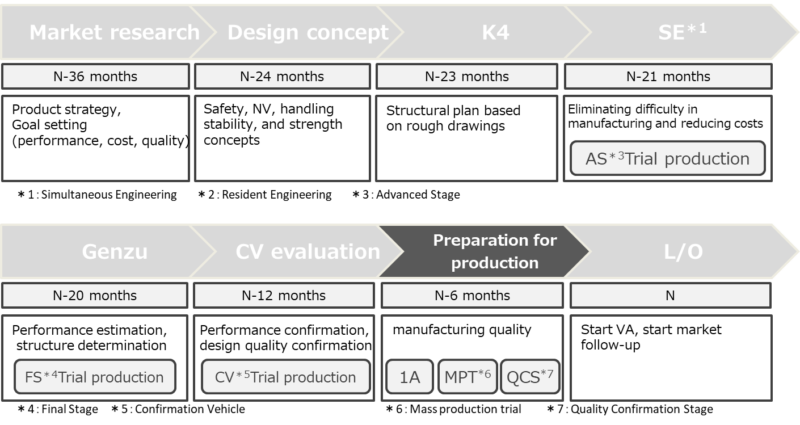
At this stage, work execution is transferred to the factory floor, where manufacturing quality issues and remaining design quality are confirmed and addressed through on-site inspection. The actual product used here is the actual model and was made through the regular production process, and is different from the CV prototype.
At this time, many related parties gather at the factory site for events ① to ③ below. This is called RE (Resident Engineering) activity because design and development engineers and engineers from parts manufacturers who are outsourced suppliers are temporarily stationed there and work with each department centered on the quality control department. There is.
①1A, 2A
They are called 1A and 2A to test the actual mass production process. At this stage, the vehicle is assembled on the actual automobile production line for the first time, and manufacturing problems are identified and countermeasures are determined.
②MPT
There is an event called MPT that checks the parts that have been modified based on the feedback obtained at 1A. Since quality issues have been largely eliminated, the main focus is to increase the number of units produced on the production line and confirm that there are no manufacturing issues.
③QCS
As this is an event to determine the start of mass production, there are no manufacturing issues remaining at this stage. A final quality check will be made.
8. Vehicle L/O
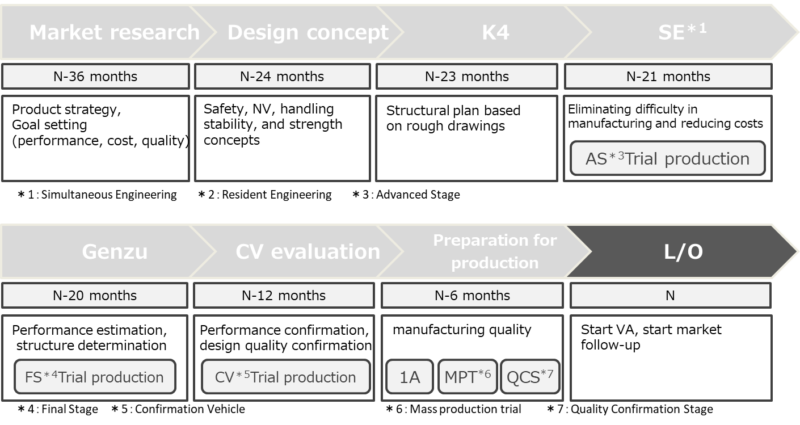
It is called L/O (Line off) because the vehicle actually leaving the line for the customer. It is also called SOP (Start Of Production).
From this period, market follow-up will begin to collect customer feedback in the market. We check to see if there are any quality issues due to special usage, and if there are any improvements that can be made in the development of the next vehicle.
Additionally, VA (Value Analysis) activities have begun, and cost reduction activities through design reviews will continue even after mass production begins.
Lastly
I think Toyota’s vehicle development approach is characterized by SE activities that involve working with suppliers to improve performance and quality. The term concurrent engineering is commonly used to mean the same thing as SE activities. This type of development flow is especially effective in cases like automobiles, where tens of thousands of parts must be assembled and assembled.