トヨタ自動車が品質の良い製品(自動車)を生み続けられる理由を開発フローになぞらえて解説します。様々な技術系職場に応用可能と思いますので、ご参考ください。
はじめに
次の図をご覧ください。これがトヨタ自動車の製品開発のフローとなります。これらを一つ一つ解説して参ります。
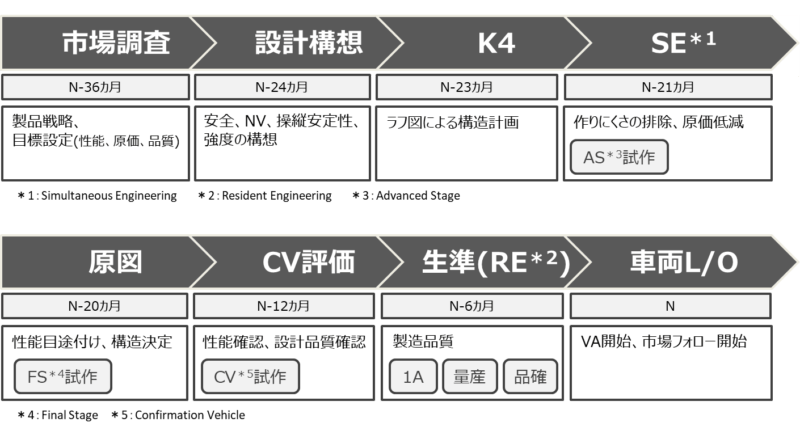
1. 市場調査:量産開始36カ月前
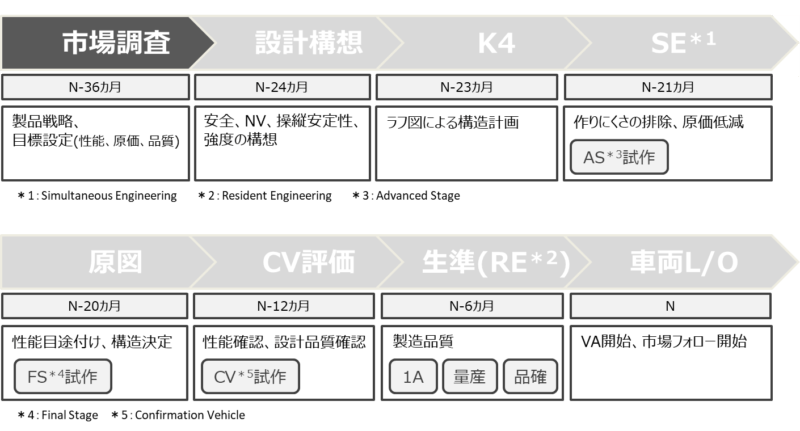
商品企画及びそれに先立つ新規開発予定車種のためのコンセプト造りのことをFSC(Future Scenario Concept)と呼びます。量産開始の3 年から4 年前の時期に始まり、調査部が作った将来の社会像(=先読み)に見合うような自動車のコンセプトを1 年程度かけて営業企画や海外事業所から集めます。ここでは具体的なスタイリングには言及せず、ユーザーにどのような価値を提供すべきかという視点が重視されます。
そして公募によって集められたコンセプト案を3~5 つまで絞り込み、経営陣へのプレゼンへと進みます。この時点では外観も検討されており、ある程度自動車としてのイメージができる状態になっています。経営陣の評価を経た後に、開発へと即座に進む場合、翌年まで持ち越しになる場合、そして廃案になる場合という3 つの選択肢から結論が出されます。
FSCを通過した案はCP(Concept Planner)へと引き渡され,商品企画段階へと進みます。実際に案件がエンジニアリングの総責任者であるCE(Chief Engineer)に渡された時点から製品企画になりますが、実際にはこれら2 つの企画段階を明確に分けることは難しいようです。
製品企画の開始後、実際の製品を実現するために、製品の目標原価、目標性能、目標品質を決定します。その目標値は、競合他社の水準を徹底的にベンチマークして今後(開発車両L/O時期)の水準を予測し、それらと戦えるように設定します。
2. 設計構想:量産開始24カ月前

量産開始まで2年を切ると、設計構想の段階に入ります。ここでは、安全、NV(Noise and Vibration)、剛性(操縦安定性)、強度という4大性能をどの水準に定めるかがエンジニアリングの視点から検討されます。
3. K4(構造計画):量産開始23カ月前
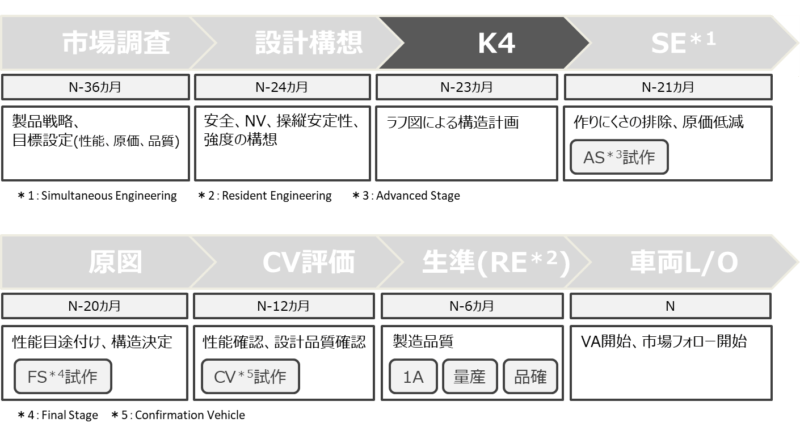
この段階に入ると種々の性能を満足するよう、断面図やポンチ絵などを基に検討が開始されます。この段階では基本的にはサプライヤーが参画していません。したがって、細かい製造性のフィードバックができないためラフ検討です。しかし、性能という観点ではここで大きな間違いがないように、類似の事例などを活用した相似設計などの机上検討により設計見積もりされます。
4. SE(Simultaneous Engineering):量産開始21カ月前

この段階での主目的は、設計品質を評価して「造りにくさを排除すること」です。製品仕様の見直しにより、造る人が造りやすい仕様にすることが、バラツキのない安定した製造品質を保証することの原則だからです。もう一つの目的は、「原価低減活動」です。設計開発部門には、企画段階で開発目標値に加えて厳しい原価目標が与えられているため、設計開発部門はこの原価目標を達成するために、さまざまな検討(VE活動)を実施します。生産部門も自らの品質目標や製造作業への影響の度合いなどを考慮して、仕様変更による可能な限りのコスト削減策を提案し、総合的な原価低減活動を展開することになります。
K4からSEにかけて、AS(Adcanced Stage)というイベントで車両が試作され、基本性能が満足するかを確認されます。
SEでの大きな特徴は、次の2つ (1)外注仕入先の参画、(2)生産技術部の参画です。
(1) 外注仕入先の参画
部品メーカの専門技術を活用して、設計そのものをアウトソースすることも頻繁に行われます。自社の設計室は社員よりも、外注仕入先の設計者のほうが多いという事態もあり得ます。開発初期段階から、外注仕入先の協力を得られるかが、SE活動成功の鍵といえます。品質保証と原価低減を、造る側である外注仕入先や社内の製造部門と協議しながら、設計開発段階での製品仕様を固めていくSE活動は、「デザイン・イン」と呼ばれています。
(2) 生産技術部の参画
工場の生産準備部門の業務を、設計開発段階へ前倒しして行うことです(フロント・ローディング)。開発の各ステップにおいては、生産に関連する組織も数多く関与するようになります。工場の品質管理部や製造部、生産設備と工法を開発する生産技術部、さらに部品を製造してくれる外注仕入先です。これらの組織が、各々の立場から設計開発の仕様をチェックし、改善要求を出すことになります。
トヨタ自動車は1996年頃からデジタルエンジニアリングによるコラボレーション、名付けて「V-Comm(Visual&Virtual Communiacation)」に取り組んできました。車両開発の前後工程のコミュニケーションを画期的に向上させることにより、試作段階で摘出していた問題の解決を設計段階へ前出し削減して出図品質を向上させ、開発期間と費用を削減させようということを狙いとした活動です。DA(デジタル・アセンブリ)と呼ばれ、次の代表的な事例で解説します。
① 作業性DA
作業者の動作をデジタルマネキンでシュミレーションし、試作車でのチェックをしていきます。
② 見栄えDA
内装部品間の合わせやボディの合わせなどモックアップや部分モデルでは十分検討できない細部の見栄えをチェックします。
③ ワイヤーハーネスDA
ワイヤーハーネスは難物であり、以前は開発の最終段階で多くの異音問題を解決せねばならなかった部分をここで潰しこんでいきます。
5. 原図:量産開始20カ月前
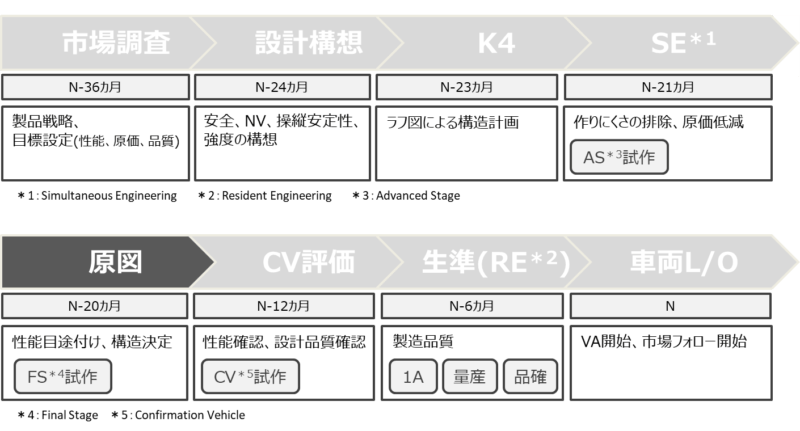
次のCV(Confirmation Vehicle)試作のイベントでは、本型品による車両での性能・品質確認になるため、サプライヤーが製造準備に入るための最後の確認段階です。SEまでに大抵の性能・品質は作りこまれており、製造性を確保するための最後の詰めになります。
SEから原図にかけて、FS(Final Stage)というイベントで車両が試作され、詳細な性能確認がされます。昨今ではCAE技術の向上により実機でなくとも性能確認できることから、FS試作は実施されなくなってきているようです。
6. CV評価:量産開始12カ月前
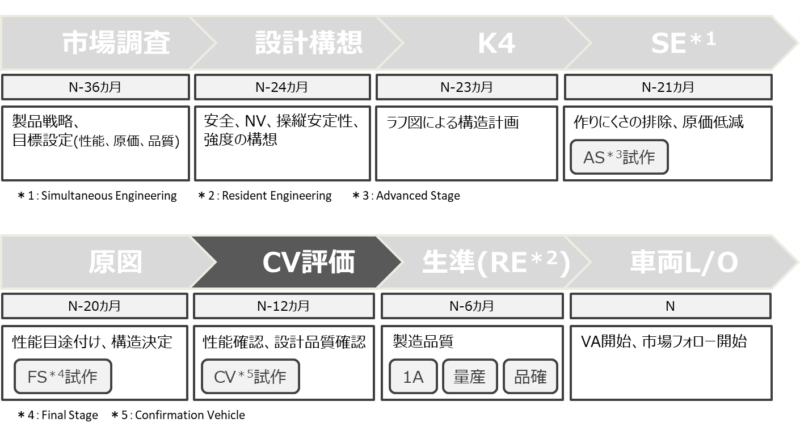
設計の狙い通りの性能が達成できているか、品質に問題はないかを本型品による性能確認車を使って各種試験が行われます。また、工場での組み立てに問題がないか生産性も確認します。
ここで本型品が要求される理由は、品質を作りこむためです。次の「生準」に入ると、これまでの技術部門から製造部門にハンドオーバー(受け渡し)されますので、確実に技術的な設計変更(型修正)を生準に織り込まなければなりません。
7. 生準(RE:Resident Engineering):量産開始6カ月前
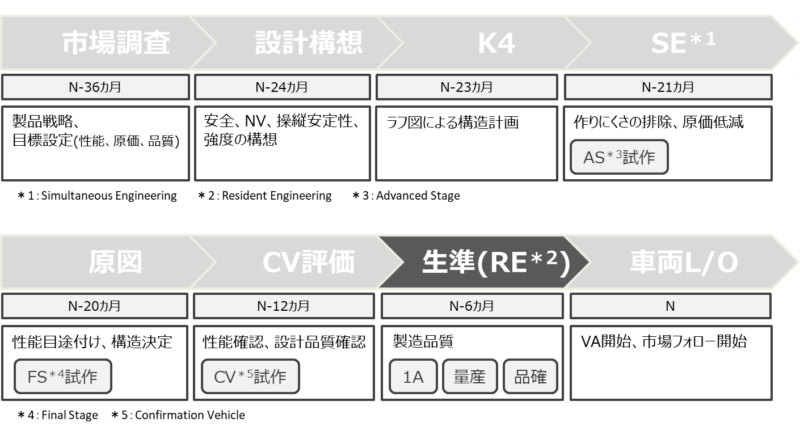
この段階では業務遂行が工場の現場に移されるため、ここでは、製造品質問題と残存している設計品質に対し、現物確認によって確認と対策が行われます。ここで用いる現物は、本型および本工程(正規生産工程)で作られたもので、CVの試作品とは異なります。
この時、工場現場には以下の①~③のイベントでたくさんの関係者が集まります(主に①)。設計開発の技術者や外注仕入先である部品メーカーの技術者が一時的に常駐して、品質管理部を中心とした各部門と活動することから、RE(Resident Engineering)活動と呼ばれています。
①1次号試(1A)、2次号試(2A)
実際の量産工程(号口)を試行するため、1次号試(1A)、2次号試(2A)と呼ばれます。この段階で初めて実際の自動車製造ラインでの車両組み立てが実施され、製造面での問題を抽出して、対策を決めていきます。
②量確(MPT)
1Aで得られたフィードバックにより設変した部品で確認する「量確」と呼ばれるイベントがあります。ここでは品質問題はほぼ潰しこまれていることから、製造ラインでの生産台数を増やし、製造面で問題がないかの確認が主となります。
③品確(QCS)
量産開始を判断するためのイベントのため、この段階では製造面でも問題が残っていることはありません。品質の最終確認が行われます。
8. 車両L/O
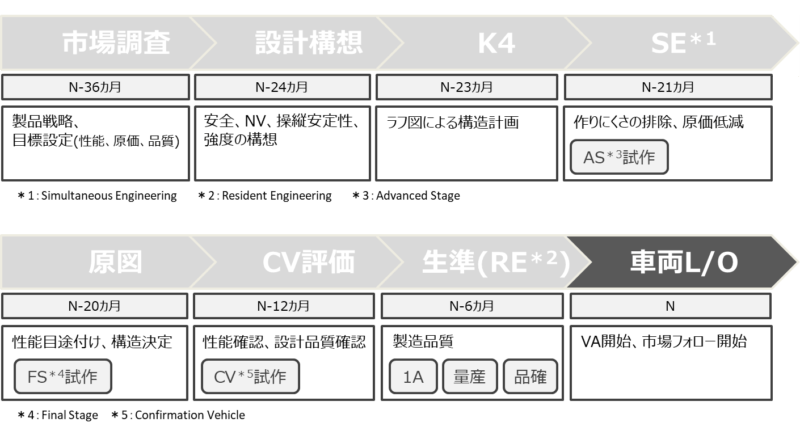
実際にお客様にわたる車両がラインを離れることから、L/O(Line off)と呼ばれます。また、SOP(Start Of Production)とも呼ばれます。
ここからは、実際に市場でのお客様の声を集める市場フォローが開始されます。何か特殊な使われ方による品質問題がないか、次の車両開発に生かすべき改善点がないか、などです。
また、VA(Value Analysis)活動も開始され、量産開始後も設計の見直しによる原価低減活動は続きます。
最後に
トヨタ自動車の車両開発の進め方では、サプライヤーも一緒に性能・品質を作りこむSE活動が特徴だと思います。なお、SE活動と同様の意味でコンカレント・エンジニアリングという言葉が一般的に使われています。特に自動車のように何万点もの部品をすり合わせて作りこまなければならない場合、こういった開発のフローが有効なのでしょう。
デジタルエンジニアリング活用による車両開発のコラボレーション
http://www.awahei.com/seizougyou/digitalengineering2.htm
トヨタ・グループの委託開発業務と組織間関係の分析
http://www2.ngu.ac.jp/uri/syakai/pdf/syakai_vol4904_07.pdf
トヨタ式 最強のモノづくり「サイマルテニアス・エンジニアリング」
http://manage-assess.net/toyota-se.pdf